The Plan
One of our very first in house designed products (working name: “the wall hook”), started with a simple idea that lead to lots of research, sketching, and modelling. After much work, we finally reached a potential look for the design. In last week’s post, we showed you that concept. Today, on this Friday the 13th, we are talking about the professional guidance that takes our ideas from paper to real life. This guidance is provided by makers who can tell us whether our minimal design can be made, if the design needs to be changed, or if we need to go back to the drawing board. It’s a stressful and exciting phase for us. Let’s get into it!
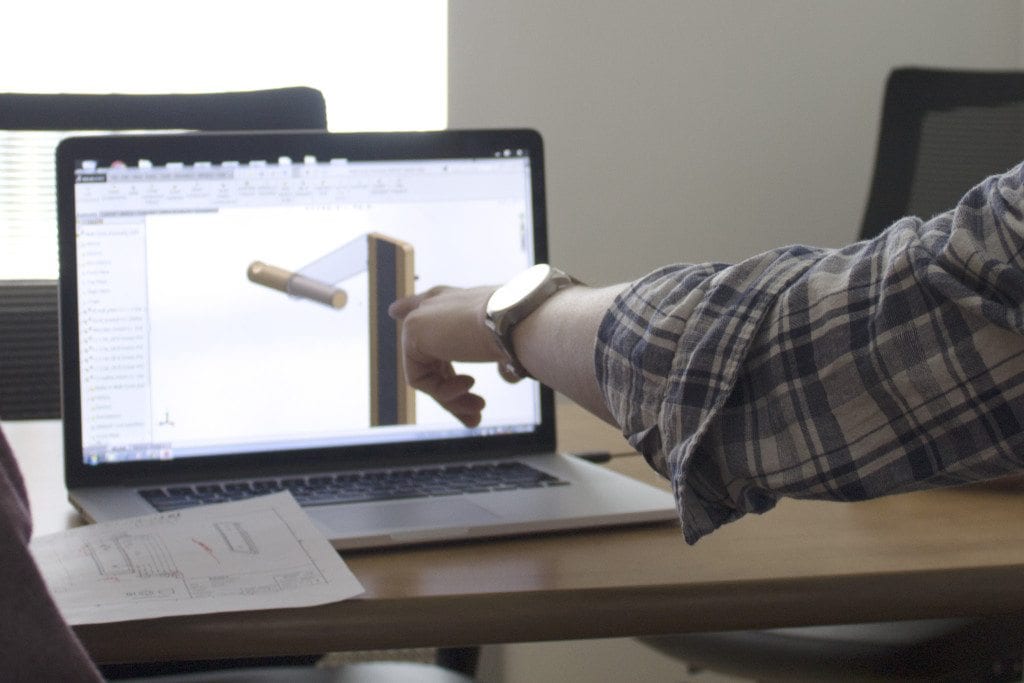
The Makers
If you take a look around your house, almost everything in it has been created by one or more makers. A maker is exactly what it sounds like – someone who makes something. Most makers specialize in a certain material (like wood or metal), or a certain process (like stitching or laser cutting). A good maker has been through every issue you can imagine. For example, a metal guy will know exactly how to manipulate metal — bending, cutting, welding, you name it! As designers, we’re the generalists – we’re good at defining user needs, functions, and aesthetics. But ultimately, we need to have a conversation with the guy in the shop cutting the metal to figure out the details that will make our product come to life. Last week we mentioned the interest of possibly having multiple components in our hook while still relating to its needs. It needs to connect to a wall, hold a heavy object like a bike, and do a little more than that too. That led us to contact different makers based on the material properties we were looking for: strong, high quality, and easy to maintain.
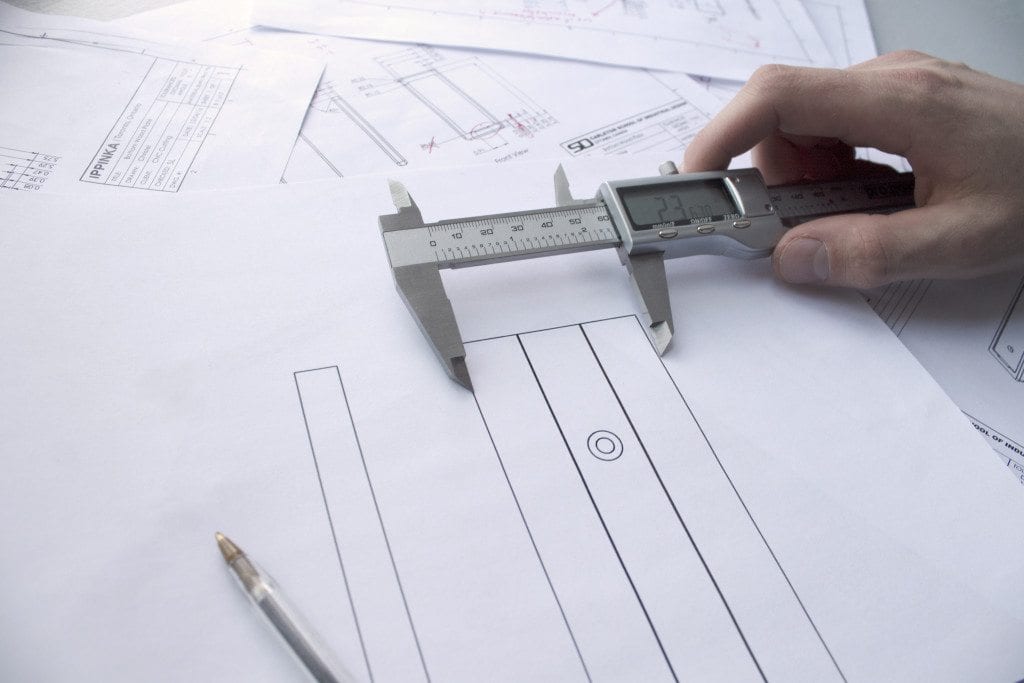
Feedback
After sending our makers all of the requirements, a brief product description, some technical drawings, and an explanation of ideas, they provided us with feedback about materials, timelines, costs and suggested changes. The makers we contacted had advice that influenced the aesthetics and the durability of the hook. They suggested softening the edges of our overall shape, selecting materials that could be easily maintained and beefing up the strength of the hook component. Good feedback is essential, especially if you want to hang a heavy bike as elegantly as possible without scuffing up your walls! Now what to do with all these suggestions?
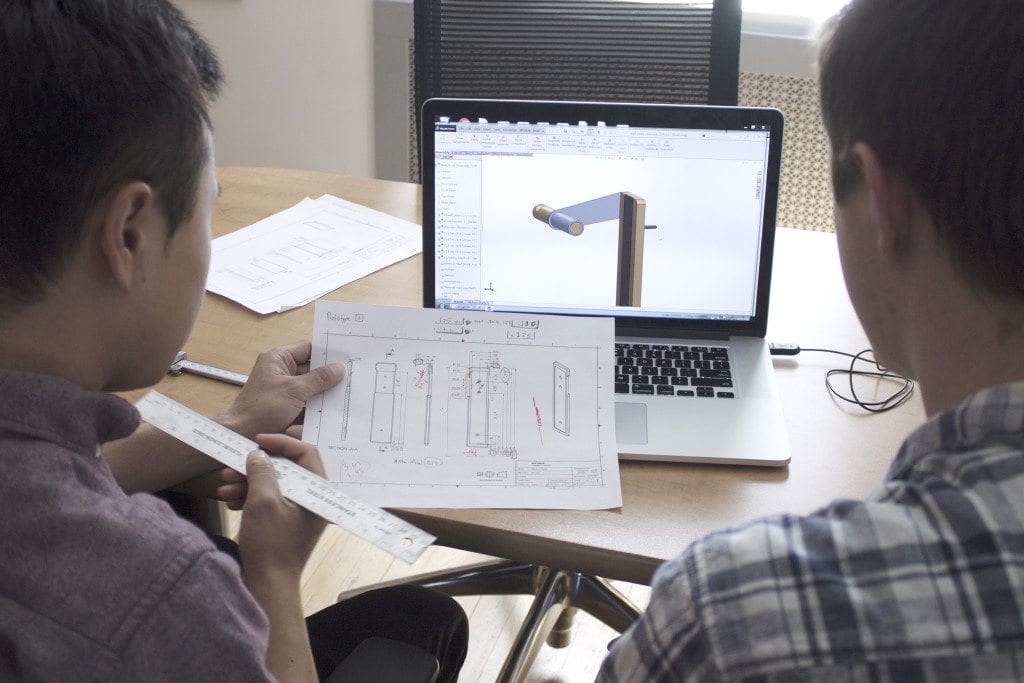
Refinements
To move forward, we implemented some of the makers’ suggestions or shall we say, we established a plan for the design that agreed with our design sense as well as the makers’ manufacturing processes. This made our design better aesthetically and functionally. Having rounded edges was easier to make, but also made our design look less severe. Researching durable materials for the hook component made it stronger, while also helping us refine the proportions of the other components. A necessary structural change can sometimes be an opportunity for us to reconsider the look and feel of the design. It’s what makes design exciting: finding a harmony between the form and the function.
So what are our mystery materials? Well it is Friday the 13th, and even though we aren’t superstitious people (we swear), we’d rather not jinx anything. So let’s hold off until next week, when we will reveal the materials of our wall piece!
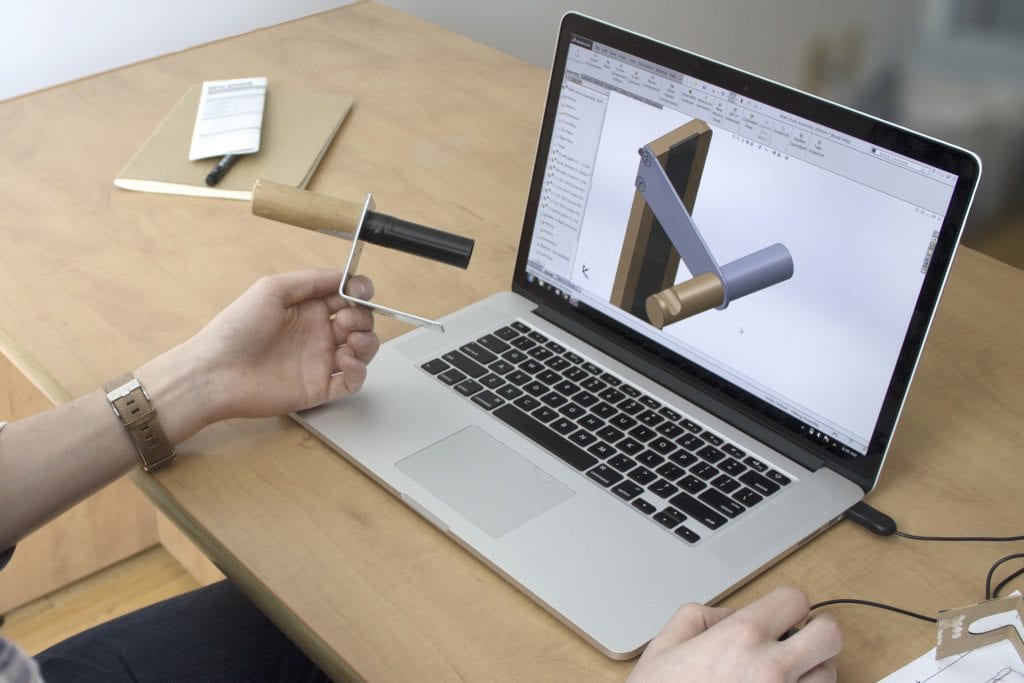